Case Study: How Albertsons Reduced Costs and Boosted Productivity with Preprinted Pallet Labels
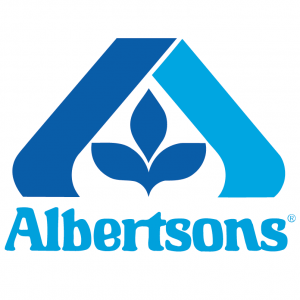
Albertsons Companies Inc. began in 1939 with a single, small grocery store in Boise, Idaho. Today, the company has successfully grown into one of the largest food and drug retailers in the United States.
It operates more than 2,300 stores, employs 250,000 people and features many well-known store brands like Safeway, Jewel-Osco, Vons, Acme Markets, Shaw’s and Sav-On, in addition to hundreds of Albertsons-branded stores.
“We’ve cut our LPN costs in half and that’s just on materials alone.”
– Curtis Walker, Albertsons Companies
Sophisticated Distribution Network
To serve its many stores, Albertsons operates a network of 15 advanced regional distribution centers (DCs), ranging in size from 500,000 to 2 million square feet. These are full-line warehouses that store millions of items such as dry goods, produce, deli foods and meats for delivery to its retail stores.
“It can be a pretty fast-paced environment,” noted Curtis Walker, an Albertsons technical analyst based in the North Salt Lake, Utah, distribution center, which services 88 stores across Utah, Montana, Wyoming, Oregon, Nevada and Colorado. “There is a steady flow of inbound and outbound shipments, each with pallets of inventory – including refrigerated and frozen goods – that need to be received, moved, picked, packed and shipped. It’s constant.”
“ID Label has been a great partner for us. We get great service, quality labels and they’re very responsive.”
To keep pace with business demands, the company is in the middle of an important, multiyear systems conversion to enable its distribution centers to operate under a single, standardized warehouse management system.
Each DC conversion can take months, but the benefits to Albertsons are significant. These include more efficient, optimized processes and labor allocation across its facilities, reduced store delivery times, improved order accuracy, better inventory tracking and balance, and reduced operational expenses.
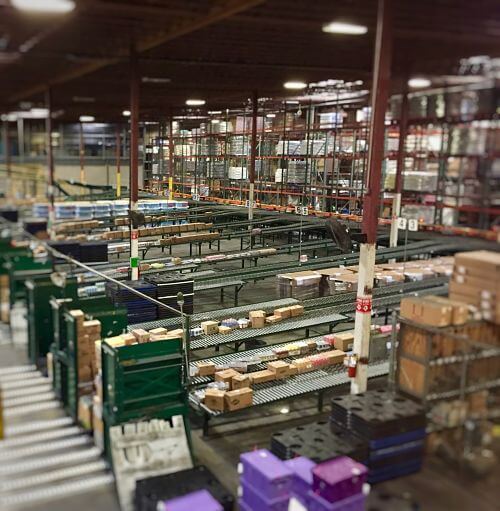
The Vital Role of Barcode Labels in a Food Distribution Center
In Albertsons’ complex, multiple-facility environment, barcode labels serve a significant role.
“They’re absolutely critical,” Walker said. “Every item, every pallet, every rack has a barcode label that contains vital product and location information. Nothing moves without a label on it.”
In the past, Albertsons printed its LPN/pallet labels in-house using direct thermal labels. But it was an expensive, inefficient process.
“The materials, equipment and maintenance can really add up,” Walker said. “And it’s inefficient for our warehouse workers to constantly go back and forth to the computer, then the printer, then out to the floor or dock to label and inventory items – and then repeat the process all over again.”
On average, each Albertsons DC goes through approximately 1.2 million LPN labels each quarter.
Making the Switch to Preprinted LPN Labels
Walker was familiar with the benefits of preprinted barcode labels, having employed the solution while at SuperValu (which previously encompassed the Albertsons brand).
He did a cost-benefit analysis and recommended the change to preprinted LPNs from ID Label.
“We’ve cut our LPN costs in half and that’s just on materials alone,” Walker said.
He estimates a savings of $12,000 for just one DC, which will grow as more DCs are added to the program.
“There are additional cost savings on printer maintenance and supplies like print heads and general wear and tear on the equipment because we’re using them less.”
Warehouse Productivity Boost
Albertsons’ DC workers also like the preprinted label solution.
“They’re more productive because they’re on the floor more,” he said, noting that they’re not constantly going back and forth to the printer to run more labels.
“As significant, we’ve virtually eliminated problems and downtime associated with computer system issues, software hiccups and printing errors due to system-generated numbers and labels that don’t always move well,” he said.
ID Label: A Solutions Partner
Distribution centers in Utah and Oregon are currently taking advantage of the ID Label LPN program. Walker expects other DCs to standardize as each converts to the company’s new warehouse management system.
“Every item, every pallet, every rack has a barcode label that contains vital product and location information. Nothing moves without a label on it.”
In addition to LPN labels, Albertsons is also working with ID Label to supply:
- Color-coded 4 x 6-inch pallet identification labels (printed on ID Label’s new digital inkjet presses) to help store employees quickly identify pallet content as it arrives – for example, to indicate items pertaining to a store promotion or advertised sale
- Store shipment identification labels to help store managers track and manage items and inventory
“ID Label has been a great partner for us,” he said. “We get great service, quality labels and they’re very responsive. They even have a Make-and-Hold program that helps me manage my LPN inventory and further reduces my per-unit costs.”
Interested in learning more? Visit our website or contact us today.
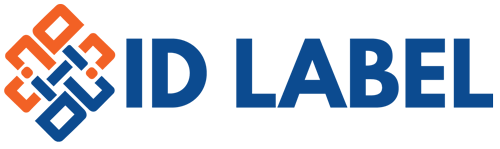
Tags
Recent Posts
- How to Remove a Rack Label: A Step-by-Step Guide
- Eliminate the Hassle of Removing Outdated or Damaged Warehouse Labels
- The Essential Role Labeling Plays in Food Traceability
- Ask the Expert: Should I Choose Paint or Tape to Mark My Warehouse Floors?
- Scott Bender Joins ID Label as Vice President of Sales