Barcodes: The Foundation of New Warehouse Data Capture Technologies
Warehouse management systems have come a long way since the mid-20th century invention of the barcode, with exciting technologies that range from the real-time tracking capabilities of radio-frequency identification (RFID) to the advanced robotics of autonomous systems. But the barcode is far from obsolete.
Meegan Johnston, business development manager at ID Label, said: “Barcode is the original data capture technology, so it acts as the foundation of all other data capture technologies. Even robotics and some of the other autonomous technologies tend to rely on scanning a visual code.”
Barcodes Get the Job Done
Given the resources and investment required to implement cutting-edge tech, it’s estimated that only 11% of warehouses identify their picking and packing process as “highly automated.” Even if those numbers go up, optimal warehouse management still hinges on the barcode’s active capture capability and human support.
Let’s take a look at some of the industry’s new and emerging data capture technologies and how barcode labeling enhances their capabilities.
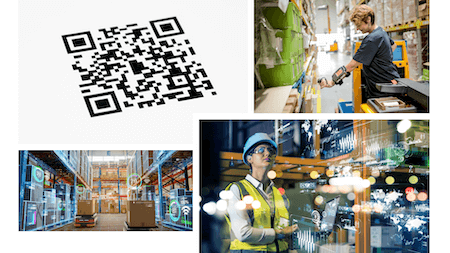
Warehouse management systems have come a long way since the mid-20th century invention of the barcode, with exciting technologies that range from the real-time tracking capabilities of RFID to the advanced robotics of autonomous systems.
“Companies can spend millions on exciting, cutting-edge technology, but if you don’t have your customized, inexpensive barcode labels, you won’t get the value out of your automation investment.”
– Meegan Johnston, ID Label
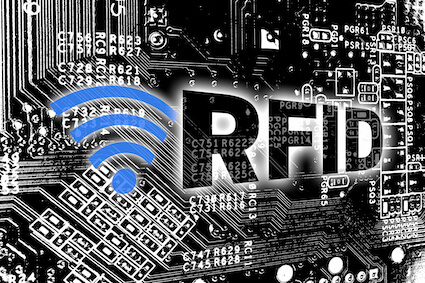
Pros and Cons of RFID
RFID technology is noteworthy for its capability to provide real-time tracking of items in a building or throughout the supply chain. Some warehouse managers choose to set up readers that form a virtual grid for item tracking, or they use RFID to track when items arrive, move within, and leave a building. While this capability is attractive in some scenarios, it’s important to conduct a full cost-benefit analysis when considering implementation of any new or emerging technology.
In addition to real-time tracking, some pros of RFID technology include:
- Enhanced security when system is operational
- Durability when exposed to elements such as liquid
- Capability to scan multiple items
The more complex a system becomes, however, the more likely it becomes for errors to occur. There are some real cons to implementing RFID, including:
- Increased expenses of RFID readers, with overall costs that can reach ten times more than using barcode scan guns
- Potential for decreased accuracy and readability as compared to barcode
- Potential for liquid, metal, or other material to interfere with system signal
- Increased time and effort to implement and maintain system
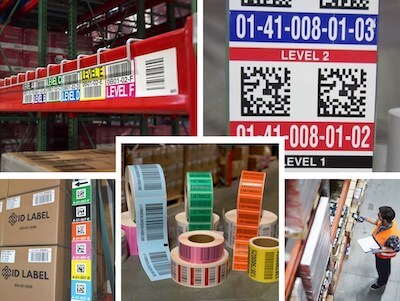
Barcodes: Cost-Effective, Ubiquitous, Proven
Some warehouses are dipping a toe into this new tech by installing RFID chips into their handheld barcode scanners for enhanced security. However, visual barcoding tends to be much more accurate and more cost-effective with a higher ROI for most warehouse operators.
What’s more, these complex systems still rely on both barcode and human support to function optimally.
“That’s where ID Label comes in,” Johnston said. “We can develop a warehouse labelling system that will provide that lynchpin between your database and your physical inventory.”
ID Label’s barcode solutions can include:
- Permanent or repositionable adhesives like Clean Release™ labels
- Magnet-backed labels
- Overhead location-identification signage
- Ultra-durable labels like BullsEye™
- Multilevel and color-coded labels
- Easy relabeling solutions like Beam Renew™
Voice and Wearable Solutions
Maximizing efficiency is the name of the game for voice and wearable technology, designed to function alongside a human worker, providing direction for picking, taking away guesswork and human error. They also allow warehouse managers to track the functionality of their systems without following workers around and micromanaging.
“But you still need a human being doing the work in a way that a machine just can’t,” said Johnston. “At this point, there’s no substitute for human intellect when it comes to decision making and spatial realization.”
Wearables help the worker get to where they need to be, but they still scan a physical barcode to verify the pick.
Voice pick can function as a combination of these two capabilities. The worker can speak directly to the system with numbers or symbols that are imprinted on the label to double check a location or item pick.
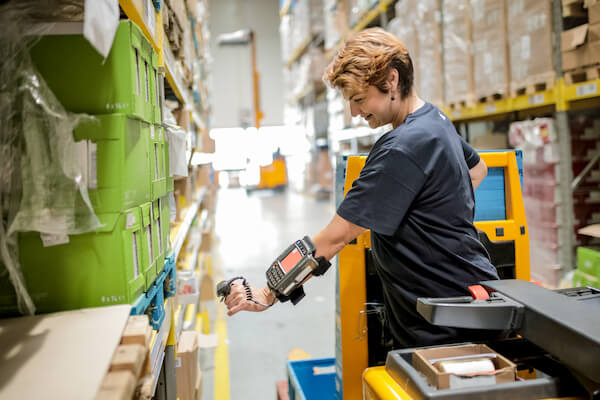
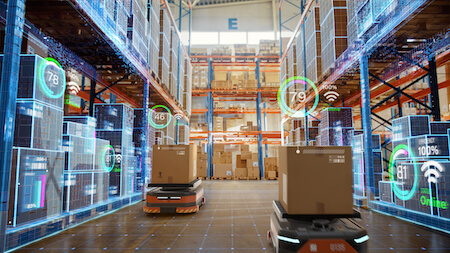
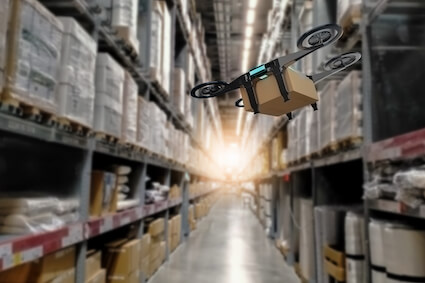
Robot and Drone Possibilities
Robots are on everyone’s minds across industries – chiefly for the concern that they could replace human jobs. When it comes to warehouse systems, especially for the large operations beginning to use robot and drone technology, there’s still plenty of work to go around.
“Robots are currently fulfilling a workload that supply chains aren’t able to fill with human beings,” Johnston said. Using robots in warehouses without concern of massive job replacement is exciting, offering the best of both worlds. If robots supplement the work that humans are doing, it gives humans the option to begin in entry level positions and move up within the industry.
Interacting with Warehouse Workers
Robots work within the warehouse in a multitude of ways, like self-propelled carts or pick-to-person. In some pick-to-person systems, the robot follows a grid laid out on the floor with barcode labels – the robot scans, orients itself, and knows it has to follow the grid pattern to pick an item. This gives the employee the ability to focus on problem-solving. Warehouses get machine-like efficiency combined with human intellect.
Drone technology works particularly well for cycle counts or inventory. Instead of having a team of people scanning barcodes, the warehouse drone can fly through at any chosen interval and perform cycle counts.
At the core of both robot and drone technology is proper labeling. Clean Release™ can offer a lot of flexibility for systems that implement drone, robot or any other kind of technology, as it can be repositioned as needed. The important thing is to determine which solutions will interact best with a particular warehouse operating system. “Companies can spend millions on exciting technology,” Johnston said, “but if you don’t have your customized 25-cent barcode labels to scan, you won’t get the value out of it that you want.”
Finding the Right Solution
Developing an efficient labelling system includes consideration of a multitude of factors like temperature, environmental changes, outdoors vs. indoors, and physical interaction with the label. ID Label can be of service no matter what warehouse system is in place, what inventory is being handled, or what warehouse technology is being utilized. ID Label’s experienced team will work with all of those elements to find the best solution.
“Labelling is one of the last things people think about, but today it’s one of the most important factors in how well your system is going to operate,” Johnston said. “Without a scannable barcode, an easily readable label and the proper label solution, you’re going to lose seconds, minutes or even hours. If the system and tech are both in place, data capture technologies are going to be exponentially more powerful.”
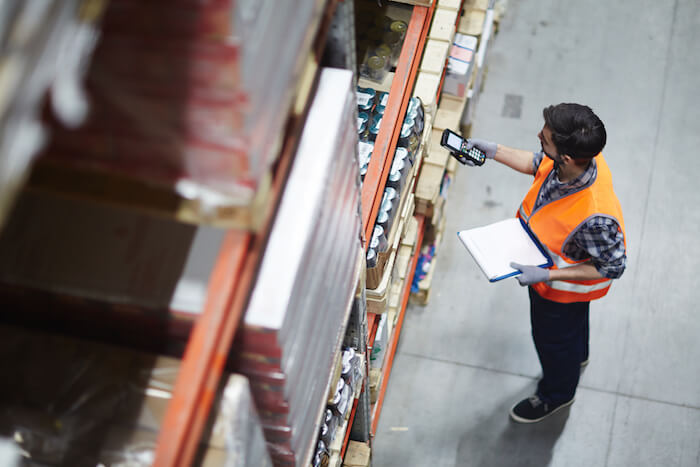
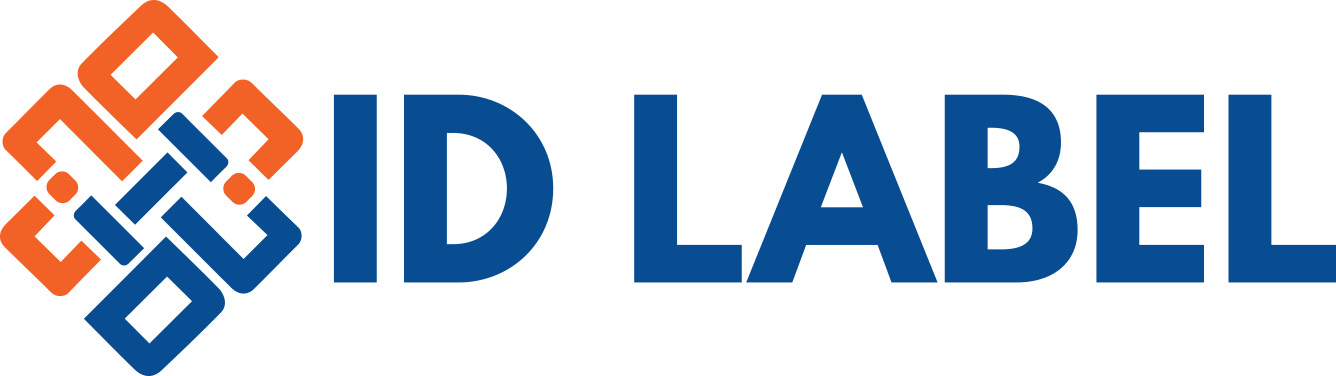
The ID Label Advantage
ID Label manufactures extremely durable warehouse labels. Our materials have been tested and used in warehouse operations around the globe.
We also provide warehouse signage and turnkey nationwide installation services to provide a complete solution to our many clients who rely on us for all their warehousing needs.
Interested in learning more? Contact us today.
Tags
Recent Posts
- How to Remove a Rack Label: A Step-by-Step Guide
- Eliminate the Hassle of Removing Outdated or Damaged Warehouse Labels
- The Essential Role Labeling Plays in Food Traceability
- Ask the Expert: Should I Choose Paint or Tape to Mark My Warehouse Floors?
- Scott Bender Joins ID Label as Vice President of Sales